If you’re a distiller, brewer, microbrewery owner, or home brewer, you’re probably familiar with the term “tri-clamp.” Tri-clamp fittings are essential components in the brewing and distilling industry, used to securely connect different pieces of equipment. In this blog post, we will delve into the basics of tri-clamp fittings, examples of their usage, their benefits, how they work, and how to measure their size.
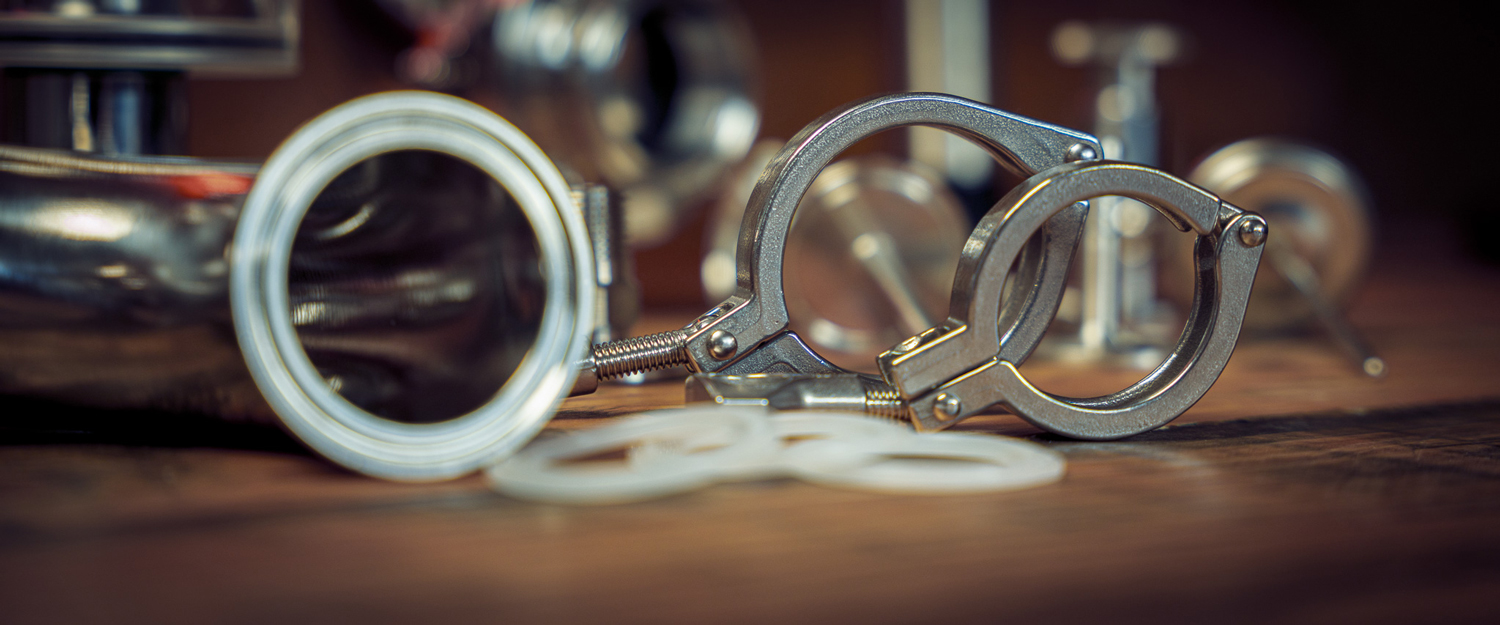
What is a Tri-Clamp Fitting?
A tri-clamp fitting, also known as a tri-clover fitting, is a crucial element in sanitary connections. They are utilized across the food, beverage, and pharmaceutical sectors. At its core, the tri-clamp fitting is engineered to facilitate a robust and hermetically sealed union between two pipes or equipment segments. This specialized fitting comprises a trio of primary components:
- A flexible gasket
- A sturdy clamp
- A ferrule (essentially a metal ring or collar).
The essence of its design lies in its simplicity and effectiveness in establishing a seamless and secure connection. The gasket between the two connecting ferrules acts as the sealing agent, preventing any leakage and ensuring the system’s integrity. This is complemented by the clamp, which encircles the ferrules and gasket, applying the necessary pressure to fortify the connection. The ferrule serves a dual purpose, supporting the pipes or equipment, and the polished surface minimizes fluid resistance. Promoting efficient flow within the system.
What sets the tri-clamp fitting apart is its adaptation for easy assembly and disassembly. This feature caters to industries where cleanliness and equipment hygiene are paramount. It allows for quick disconnection and reconnection of components, facilitating thorough cleaning and sterilization processes without requiring specialized tools. This combination of leak-proof security, ease of maintenance, and hygienic design positions the the fittings as an indispensable ally in maintaining sanitary conditions. Especially in environments where the purity and quality of the product cannot be compromised.
The tri-clamp fitting’s universal design compatibility across a wide range of diameters and its ability to sustain a variety of gasket materials. Each is tailored for different temperatures and chemical exposures. Further accentuating its versatility and indispensability in creating efficient, safe, and clean production lines in the targeted industries.
The Basics of Tri-Clamp Fittings
Tri-clamp fittings, a cornerstone in sanitary process lines, stand out for their design. They emphasise ease of use and contribute to their widespread popularity. A feature particularly appreciated by professionals in the brewing, distilling, and food processing sectors.
The foundational mechanism involves the unique assembly of components. At the same time, a surrounding clamp applies the necessary compression to secure the connection. This configuration ensures a leak-proof seal and facilitates smooth fluid dynamics within the system. An attribute that enhances process efficiency by reducing the risk of contamination and preserving the quality of the product.
Integral to the tri-clamp system, Ferrules play a significant role beyond just forming connections. They are designed to provide a hygienic contact surface, minimizing areas where bacteria can harbour and proliferate. This feature is crucial in applications where sterility and product purity are non-negotiable.
Another notable aspect of tri-clamp fittings is their ease of cleaning. Given the high demands for sanitation in their primary industries, the ability to quickly dismantle, clean, and reassemble the fittings without the need for special tools is invaluable. This facilitates routine maintenance and allows for more efficient shifts between different products or batches. This significantly reduces downtime and increases productivity.
Moreover, their compatibility with various gasket materials highlights the versatility of tri-clamp fittings. This adaptability allows them to withstand various temperatures and chemical exposures, ensuring reliability and safety in various operational conditions. Whether it’s withstanding the acidic environment of a brewery or the stringent sterility requirements of a pharmaceutical manufacturing line, provide a dependable solution that meets the rigorous standards of these industries.
In essence, the basics of these fittings revolve around their practicality, ensuring secure, clean, and efficient connections. Upholding the integrity and quality of the production process.
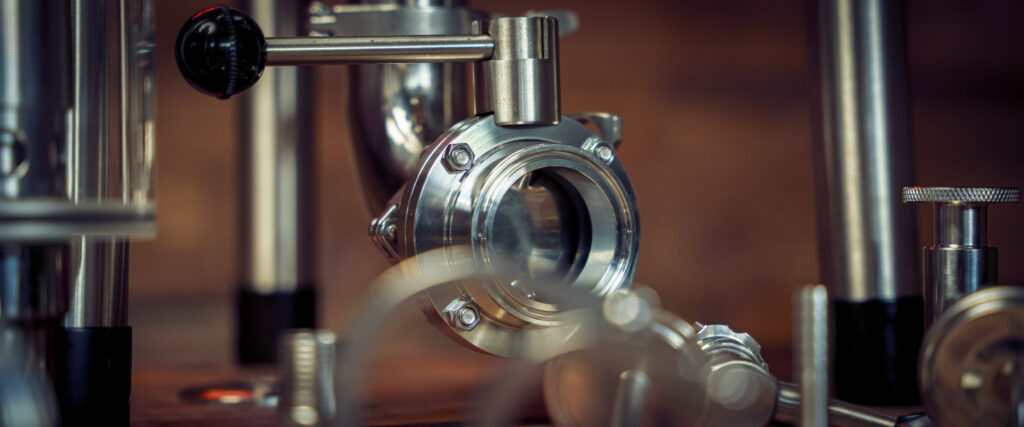
Examples of Tri-Clamp Fittings
Tri-clamp fittings are versatile, adapting to various functions with remarkable efficiency. Their applications span a broad spectrum, catering to the seamless operation of equipment in facilities dedicated to brewing, distilling, and beyond. Among the plethora of tri-clamp fitting varieties, some notable examples stand out for their specific utility and widespread adoption.
- Tri-clamp elbows are engineered to facilitate directional changes in liquid flow. Allowing for flexible piping layouts in confined spaces or around obstacles. This type of fitting is crucial in designing an efficient process line that maximizes space without compromising flow dynamics.
- Tri-clamp tees are critical in branching a process line, enabling flow distribution in different directions. This is particularly useful in systems requiring simultaneous operations or scenarios where a single source feeds into multiple vessels.
- Reducers are another vital category of tri-clamp fittings designed to connect pipes or tubes of varying diameters. They are indispensable when the process line transitions between equipment of different sizes. Ensuring a smooth flow rate and minimizing turbulence.
- Sight glasses incorporated with tri-clamp fittings offer a clear advantage by allowing visual inspection of the flow. These fittings are invaluable for monitoring the product during transfer. Ensuring clarity, consistency, and, when necessary, the presence of desired characteristics in the fluid being processed.
Each of these examples underscores the adaptability of tri-clamp fittings to meet the specific requirements of a facility’s process lines.
Benefits of Tri-Clamp Fittings
The utilization of tri-clamp fittings in brewing, distillation, and other processes requiring sanitary conditions presents a myriad of advantages. One of the foremost benefits is their contribution to heightened sanitation standards. The design of tri-clamp fittings, with minimal crevices and a smooth surface, drastically reduces the areas where bacteria and other contaminants can accumulate. This aspect is pivotal for industries where hygiene is paramount, ensuring that the quality and safety of the product are maintained.
Other significant advantages
- Ease of assembly and disassembly.
- No tools required
- Durability
- exceptional resistance to corrosion and wear.
- leak-proof seal
- Maintain consistent pressure and flow
In summary, adopting tri-clamp fittings within industry settings offers many benefits ranging from improved sanitation and ease of maintenance to durability and a secure, leak-proof connection. These advantages collectively contribute to a more efficient, reliable, and cost-effective operation, underscoring the significance of fittings in achieving and maintaining high production and product quality standards.
How Does a Tri-Clamp Work?
The operation of tri-clamp fitting centres on a brilliantly simple yet effective mechanism. Initially, the ends of two pipes or pieces of processing equipment that require connection are each equipped with a matching ferrule. These ferrules act as the interface for the fitting, designed to align perfectly with one another to ensure a smooth continuation of the piping or equipment system. The gasket is at the heart of the connection, a critical component between the ferrules. This gasket is the primary sealing element, crafted from materials selected for their chemical compatibility and temperature resilience, tailored to meet the specific demands of the process environment.
The tri-clamp comes into play once the ferrules and the gasket are correctly positioned. This circular clamp fits snugly around the outside of the ferrules, encompassing the gasket between them. The clamp is then tightened, typically by a securing mechanism such as a wing-nut or a bolt, depending on the design of the tri-clamp. As it tightens, it exerts uniform pressure around the circumference of the ferrules, compressing the gasket between them. This compression creates the hermetic seal, preventing any leakage of fluids or gases from the connection point.
The brilliance of the these fitting lies in its ability to maintain a secure and leak-proof seal while offering the convenience of quick disconnection and reconnection. This feature is particularly advantageous in processes that require frequent disassembly for cleaning and maintenance, allowing operators to easily access the system internals without compromising the integrity of the connection upon reassembly. Furthermore, the simplicity of this mechanism minimizes the risk of incorrect assembly, ensuring that the system remains safe and operational at all times. This operational methodology underscores the fitting’s value in industries where process integrity, sanitation, and efficiency are paramount.
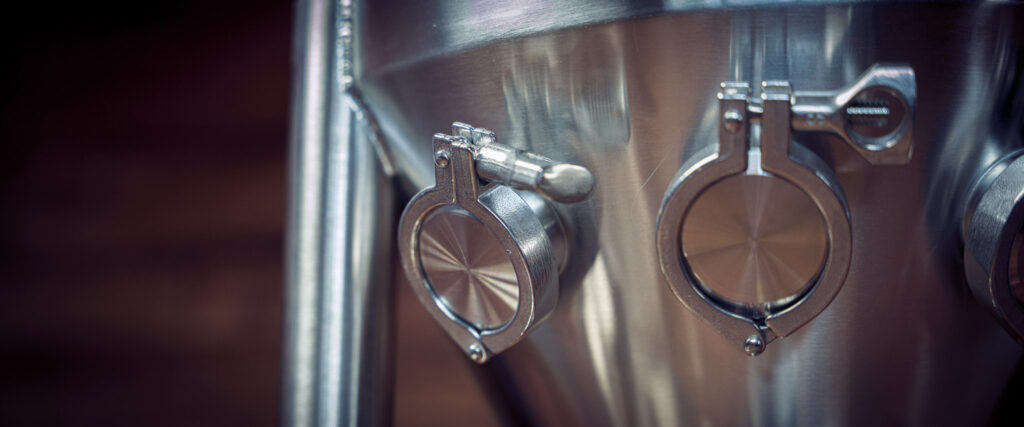
How to Measure Tri-Clamp Size
Selecting the right size of the tri-clamp fitting is a crucial step to ensure the efficacy and safety of your process system. Understanding how to measure these fittings accurately can save time and prevent potential complications during assembly. Determining the correct size is straightforward but requires attention to detail. To begin, you will need a calliper or a flexible measuring tape, tools capable of providing precise measurements. The critical measurement for a tri-clamp fitting is the ferrule’s outer diameter (OD), which should not be confused with the diameter of the pipe or tube itself. The ferrule is the circular ring the clamp encloses to form the seal.
Here’s how to proceed:
- If the system is currently assembled, ensure it is safe and appropriate to disassemble the section where the measurement is needed. If the fitting is not yet installed, prepare it for measurement.
- Take your calliper or measuring tape and measure across the centre of the ferrule to determine the OD.
- Ensure your tool is perpendicular to the ferrule to get an accurate reading.
- For callipers, align the jaws by touching the outermost edges of the ferrule.
- Using a tape measure, be cautious of its flexibility; it should hug the ferrule snugly without sagging.
- Record the measurement. It’s always a good practice to measure twice to confirm accuracy.
In the United States, measurements are typically provided in inches, and common tri-clamp sizes range from 1/2 inch to 12 inches in diameter. However, 1.5 inches and 2 inches are among the most frequently encountered sizes in the brewing and distilling industries.
Understanding that the tri-clamp size directly correlates to the OD of the ferrule—and not the inner diameter (ID) of the tube or pipe it’s connecting—is essential for making the right selection. This clarity ensures that the fittings will provide the intended hermetic seal, maintaining the integrity and hygiene of your process system. Armed with the correct measurement, you can confidently acquire the appropriate tri-clamp fitting, contributing to the smooth and efficient operation of your brewing or distillation system.
If you need to know the ferrule sizes, see the chart below.
TRI-CLAMP SIZE (ALSO PIPE OD) | FERRULE OUTSIDE DIAMETER (INCH) | MM | |
1″ | 1.984 | 50.3936 | |
1.5″ | 1.984 | 50.3936 | |
2″ | 2.516 | 63.9064 | |
2.5″ | 3.047 | 77.3938 | |
3″ | 3.579 | 90.9066 | |
4″ | 4.682 | 118.9228 |